從156.75 mm到166 mm,大尺寸硅片已經悄然進入市場,硅片尺寸增大在電池片制造、組件封裝等環節能夠實現成本節約,據了解M6電池片各制程的工藝時間與M2制程時間相差不大,因此在電池制造過程中每片大約可降低0.05元成本。
在白城等地,光伏電站中標電價已經接近平價甚至低價,大尺寸電池片投產會使光伏平價運營更近一步,2019年新建產線最基本的要求就是設備兼容大尺寸硅片的生產。更令人振奮的是今年8月中環推出了M12硅片,邊長210 mm,比M2硅片面積增加80%,單瓦生產成本將會進一步降低,M12硅片的推出是顛覆性的,大尺寸硅片終將是光伏行業的未來。
但我們也要認識到現有的設備可能無法兼容大尺寸的硅片,硅片增大后又會給設備制造商帶來新的需要解決的問題,整個制造環節都需要技術升級和突破,在這里以管式PECVD設備(如圖1所示)為例討論M6、M12硅片鍍膜時需要做哪些準備和考慮。
圖1. 管式PECVD
圖2. 單臺管式PECVD設備產能提升情況
PECVD是電池片產線上重要的鍍膜設備,制備得到的減反鈍化膜可以有效減少電池片表面反射率,增加光的吸收,同時對硅片表面和體內的復合中心起到鈍化作用。PECVD從結構上可分為管式和板式兩類。如表一所示,與板式PECVD相比,管式PECVD優點是開機率高、維護周期長、退火和鈍化效果好。綜合成本投入、后期維護等因素,新產線基本都選用管式PECVD制備減反鈍化膜。如圖2所示,從08年到19年,單臺管式PECVD的產能快速增加,未來可能出現單臺6000片以上的單小時產能。此外管式PECVD的工藝整合能力也很強,目前有些生產線已經采用背面二合一PECVD設備,將背面氧化鋁和氮化硅膜集成在同一機臺甚至同一管內進行,縮短了制程時間,減少了設備投入成本。
表一. 板式、管式鍍膜設備對比
硅片尺寸的增大一定程度上限制了單管載片量的增加。目前國內外老產線開始生產M6硅片,在改造管式PECVD設備時遇到了部分問題:
1、石英管尺寸限制
石英管尺寸的限制本質在于石墨舟尺寸的變化。在軟著陸機臺中,166 mm硅片石墨舟的高度較高,進出舟的空間位置非常小,容易發生刮蹭舟腳等問題。為了解決該問題,只有減少石墨舟的載片量或者切除一部分舟腳,改變舟結構可能會影響石墨舟的使用壽命,因此多數產線選擇了降低石墨舟載片數量的方式。
2、溫區長度限制
搭載166 mm硅片的石墨舟在高度和長度兩個方向上都有增加,長度方向上大概增加了80 mm,相當于石墨舟頭的硅片向爐口方向移動了80 mm。盡管目前從工藝結果上看影響并不明顯,但是越靠近兩端爐體的封口效果越差這是不爭的事實,爐口中心的硅片有發紅的危險。
總體來講,M6硅片鍍膜設備在M2的基礎上僅從石墨舟進出空間上做出了相應改動,干泵、流量計,射頻電源等部件并不需要相應擴大升級;那如果是M12設備呢?
圖3. 石墨舟尺寸及重量變化(從M2到M12)
為了能夠承載M12硅片,石墨舟尺寸及總重量均會發生較大改變(圖3所示)。石墨舟的總長度由156機臺的1600 mm增加到至少2100 mm。高度從200 mm增加至250 mm以上,帶片的重量從30 kg左右增加至~45 kg。超大的石墨舟需要配套超大的石英管,需要考慮水平運送機構的承重能力。現在市面上有兩種結構的管式PECVD設備——懸臂結構和軟著陸結構。如果采用懸臂結構在考慮進出舟空間的同時更要重點關注重量的增加,尤其是熱狀態下負重懸臂結構的變形,這會是懸臂M12設備的一個技術難點;軟著陸設備石英管的直徑需要設計的更大,用來保證槳的升降進出空間,相對而言,軟著陸的負重壓力較小,可以在石英管內增加支撐梁。盡管懸臂和軟著陸設備的石英管直徑在設計上有差別,設備的總高度相差并不大,當然現在的廠房高度是不能承載5管M12設備的,廠房高度需要增加~50 cm。
石墨舟的長度增加了500 mm左右,溫區長度至少要增加500 mm,溫區的長度至少要覆蓋住整個石墨舟,加長之后如果采用五點控溫可能更不容易控制工藝結果,需要增加一個控制和監測點,溫區的分布也需要根據硅片的位置做出相應規劃,盡量保證硅片不處在兩個溫區交界位置。
除了空間位置上,配套部件也需要進行升級。首先是射頻電源的選擇問題,鍍膜設備從單舟308片升級到單舟416片時,射頻電源的最大功率提升了50%,更大的射頻功率保證了鍍膜時石墨板間的電場能量密度,也就保證了大舟的鍍膜速度,從石墨舟的增量上推算,432片M12的石墨舟使用的射頻電源功率不應低于20kw。還需要注意的是,射頻功率加大后,鍍膜時的射頻電流提升非常明顯,射頻功率的計算公式為:
P=U×I×Cos(相位角)
決定射頻電壓值的主要是石墨舟同軸電纜的阻抗和石墨板間氣體的容抗,這在氣體比例相同的情況下一般是一個相對固定的值,射頻功率增加一倍,電流值也接近增加一倍。單片石墨舟和硅片上流經的電流也會增大近一倍,這種情況下可能造成射頻功率波動、卡點燒焦等一系列射頻問題。防止這種情況出現應當重新考慮石墨舟卡點的設計,增加插片機插片精度,減少在石墨舟運動輸運過程中發生的掉片翹片情況。
類似的情況同樣適用于通入流量的選定,目前鍍膜時使用的特氣流量大約在10 slm左右,按照硅片的有效面積增量來估算,M12設備的流量總通入量應該18 slm以下,基本達到了現有流量計配置的極限,如果想要給工藝調整提供余量,或者是更好的控制特氣流量精度,現有的流量計量程應增加50%左右。
通入氣體增加必然涉及到干泵的選擇,在通入大量氣體時是否還能正常調壓是問題的關鍵。我們以國內某型抽速為1000 m3/h的干泵現場的使用情況為例,統計不同抽速下通入氣體流量能夠穩定的壓力值,結果如表二所示。鍍膜的工藝壓力基本上要高于1500 mtorr,因此該抽速的泵完全能夠保證調壓成功。
表二. 流量、抽速與壓力的關系
最后講兩點大尺寸硅片設備的隱憂。首先,硅片增大后,片內的膜厚均勻性更不容易保證。從M6硅片的鍍膜情況來看,硅片幾何中心點的膜厚較低,如表三所示,隨機挑選一舟硅片測試五點的膜厚折射率,上下左右距離中心點位置約為20mm,測試結果顯示中心點位置膜厚普遍偏低1-2nm。硅片增大到M12后,中心點到硅片邊緣的膜厚差距會進一步拉大,會給工藝優化和工藝控制帶來一定難度。另外一點是增大硅片后,單片硅片的凈產出增大80%,不良的比例因為硅片面積的增加也相應增加了80%。例如原產線上碎片率為0.02%,改為生產M12硅片時,碎片率依然是0.02%,但是碎片的成本因為硅片尺寸的增大而變大了,這就要求,產能越大的設備,其設備及工藝穩定性必須提高。
表三. NAURA機臺M6硅片工藝結果
綜上所述,大尺寸硅片是當前晶硅電池行業發展的重要趨勢,也是產業制造進一步降本的必然選擇。無論是變化較為緩和的M6還是更為激進的M12,都對包括管式PECVD在內的所有設備、工藝提出了許多新的挑戰,相應參與者需要在設計環節就全面考慮尺寸變化帶來的諸多新問題新需求,才能更有效地服務行業,更好地帶動產業發展。
責任編輯:gt
-
光伏
+關注
關注
44文章
3083瀏覽量
69401 -
電池
+關注
關注
84文章
10675瀏覽量
131317
發布評論請先 登錄
相關推薦
7納米工藝面臨的各種挑戰與解決方案
半導體微電子硅片制備離不開全氟過濾PFA材料
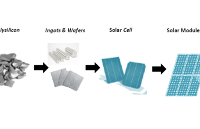
產業"內卷化"下磁性元件面臨的機遇與挑戰
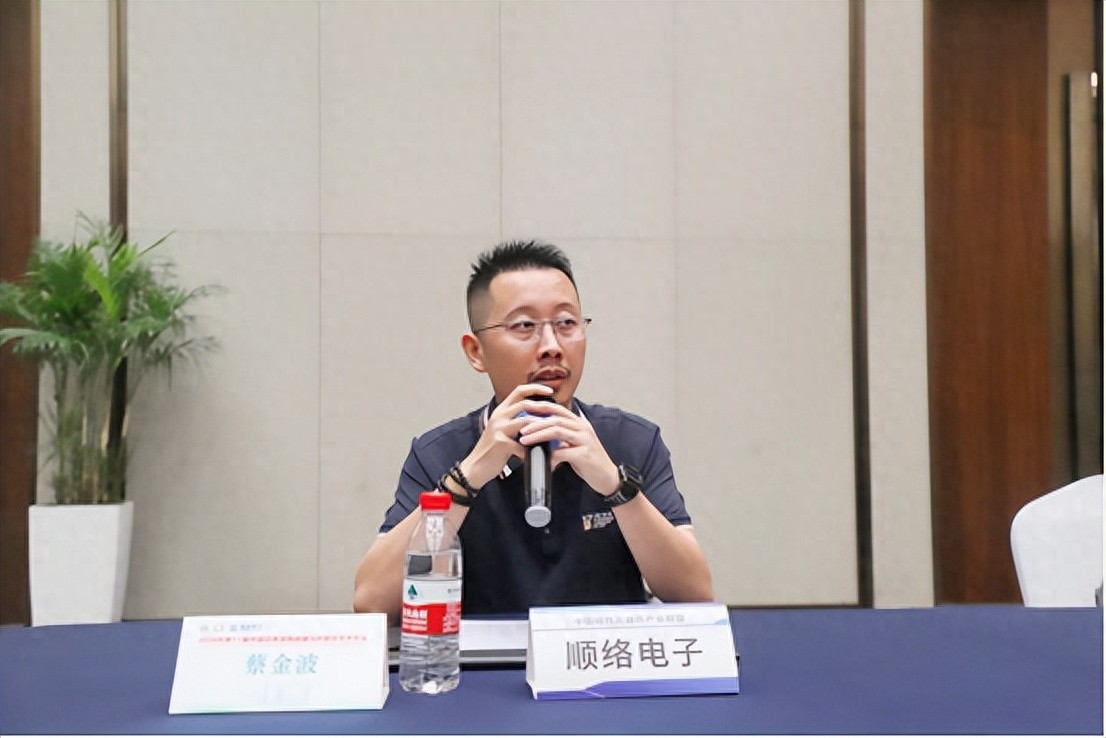
節能回饋式負載技術創新與發展
【?嵌入式機電一體化系統設計與實現?閱讀體驗】+磁力輸送機系統設計的創新與挑戰
CMOS晶體管的尺寸規則
蘋果AI時代面臨挑戰,需對戰略進行重大改變
全光網應用面臨的挑戰
人工智能芯片在先進封裝面臨的三個關鍵挑戰
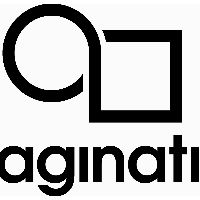
汽車雷達系統設計面臨的挑戰
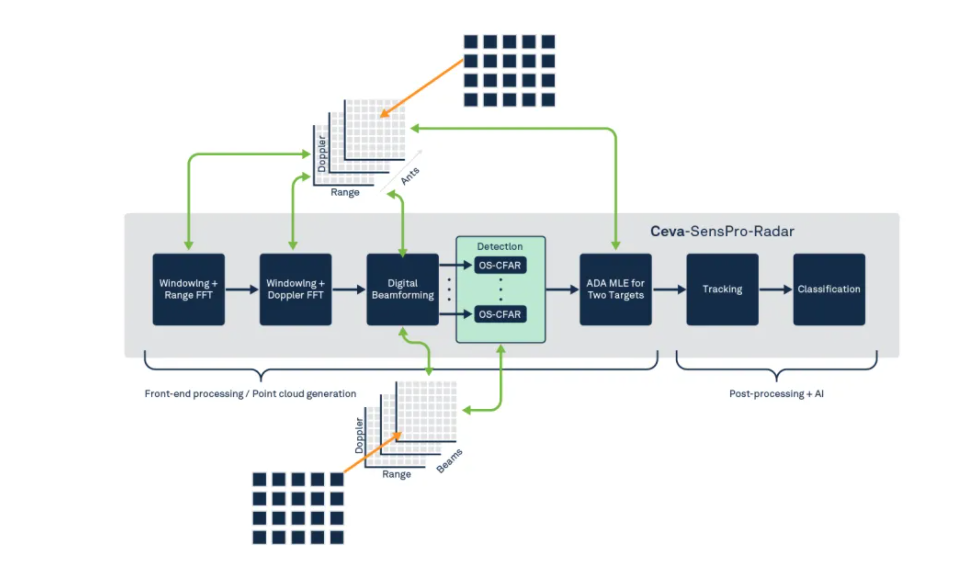
隆基泰睿硅片產品發布
硅片分選設備上的智能傳感器
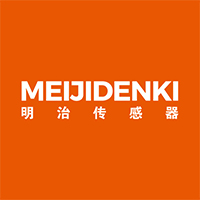
突破行業難題,硅片分選解決方案再升級!
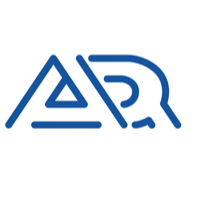
評論