實施六西格瑪管理的目標就是希望生產出的產品的特性指標的標準差要盡可能小(只調節均值對中效果有限)。
讓標準差盡可能小不是件簡單的事,它可能牽涉生產中的很多因素。生產中產生的變異這么大,到底是哪些原因形成的?通過事先安排好的計劃,有規律地去收集生產過程中的有關數據,通過統計分析,我們不但要弄清楚變異是由哪幾部分原因組成,而且要定量地給出每部分原因所產生的變異究竟在總變異中占多大的比例。我們要找出產生變異的“罪魁禍首”,并把所有對產生變異有“貢獻”的因素,按其對產生總變異的“貢獻率”排成隊,定量地列出一個需要解決的問題的順序清單,以便在選擇攻關項目時作為參考依據,這種分析方法就是我們所說的變異源分析,這一塊內容在藍皮書上有詳細介紹(參見藍皮書第三版第9章)。變異源分析是一個很大的課題,我們今天通過一個簡單的案例強調一下它的重要性。
案例
一家紡織廠用許多臺織機編織一種織物,希望織機盡量相同使得織物的強度一致。過程工程師懷疑除了同一臺織機編織的織物間強度會有差異外,在不同的織機間織物的強度也有顯著差異。為此,她隨機選擇了4臺織機并對每臺織機生產的織物進行了4次強度測量,實驗按隨機順序進行,數據如下所示:
在輸出結果中,我們主要關注的是方差分量這一塊。我們可以看到任一強度觀測的方差為8.85417(標準差2.97560),其中大部分的變異來源于織機間的差異(方差為6.95833,標準差為2.63786),占總變異比率為78.59%,剩下變異全歸隨機誤差方差為1.89583(標準差為1.37689),占總變異比率為21.41%.
這個案例的操作和解釋到此結束,現在我們再回到文章的開頭。學變異源分析不是讓大家熱衷對方差分析的深入研究,比如這里方差分量的計算,而是要去對過程變異的關注。現在強度的變異非常大,過程不良率非常高,如下圖所示:
容易看出,過程輸出中有相當大的比例落在規格限之外。過程工程師疑慮為什么這么多的織物不合格,需要報廢、返修或降格為低質量產品。答案是產品強度的差異主要源于織機間的差異,織機間性能的差異可能源于錯誤的設置、缺乏保養、缺少監管、操作員技術差、原材料有問題等。過程工程師現在需要去現場查找造成織機性能差異的具體原因,若她能找出并消除織機間差異的根源,過程產出的標準差就可以明顯減少,也許可以低到1.37689,如下圖所示。雖然不太可能根除織機間的所有差異,但是,方差分量的明顯減小顯然能大大提高所產織物的質量。
其實,看上圖和方差分量的結果,我們可以看出來,即使通過改善把織機的變異源消除,剩下的變異還是很大(變異占比21.41%),說明還可能存在其他變異來源,所以把織機問題解決后我們還要進一步分析。
吐槽一下
變異源分析背后理論涉及到方差分量的計算,詳細推導可以參考蒙哥馬利的《實驗設計與分析》,但我在這里也不得不說一下很多朋友就是因為看書才放棄了這一塊內容的研究學習,原因很簡單:公式太復雜,然而計算這一塊我們交給Minitab軟件就行了。我們需要做的是在前期:變異來源有哪些?這些因子是隨機還是固定?這些因子之間的關系是交叉還是嵌套?基于這些問題再去制定數據收集計劃,計算交給軟件,我們會解讀結果即可。
另外,變異源分析也是我們常用工具(如MSA、SPC和DOE等)的基礎,沒有變異源的調查這些分析可以說是毫無意義。
審核編輯黃宇
-
Minitab
+關注
關注
0文章
180瀏覽量
11765 -
變異源
+關注
關注
0文章
2瀏覽量
6630
發布評論請先 登錄
相關推薦
什么是源阻抗?失調電流與源阻抗分析
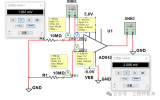
AMC1303E輸出接的Altera FPGA,通過FPGA解碼后輸出總是突然來個變異的大數據,為什么?
hspice共源放大電路仿真分析
在運放的源阻抗為二階系統的時候如何分析電流噪聲對輸入端的噪聲的影響?
受控電流源在電路中如何分析出來
受控電流源電流方向怎樣判定
電流源串聯電壓源的工作原理、特性及應用
受控電壓源和電阻并聯的電路分析
受控電壓源和電壓源串連怎么等效
受控源轉換為電阻的方法
疊加定理電壓源和電流源怎么處理
受控源什么情況下可看為電阻
節點電壓法受控源怎么處理
學員筆記:什么是源阻抗?失調電流與源阻抗分析
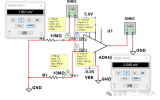
評論