一塊看似簡單的PCB電路板,背后卻是繁多的生產工序。
PCB生產工序和工藝環節
而在PCB這一系列生產流程中,匹配點很多,一不小心板子就會有瑕疵,牽一發而動全身,PCB的質量問題會層出不窮。下面整理了62種PCB電路板的不良實例,你遇到過幾種呢?
一、基材不良
1.基材不良見底板
不良原因:搬運過程中導致擦花,造成線路缺口。
不良影響:對產品走線的阻抗造成影響。
規避措施:規范作業,加強管控。
2.基材不良顯白斑
不良原因:板材經受不適當的機械外力的沖擊或局部扳材受到含氟化學藥品的滲入而對玻璃纖維布織點的浸蝕。
不良影響:影響外觀及信號的電器連接。
規避措施:采用高Tg板材;盡量減少或降低機械加工過度的振動;選擇適宜的退錫鉛藥水及操作工藝。
3.基材不良露布紋
不良原因:粘結片樹脂含量偏低或流動度大,層壓時流膠過多;或層壓時升溫升壓過快,加高壓過早,造成流膠太多。
不良影響:基板露布紋造成基板的絕緣性能下降,嚴重影響PCB板質量。
規避措施:可以采用“表料”和“里料”的作法,讓表料樹脂含量適當加大并調整相應GT和RF%等技術參數,產品在熱壓時要有足夠的固化溫度和固化時間,可以防止露布紋現象和提高基板耐化學藥品性及電性能。
二、內印不良
4.內層顯影不凈
不良原因:油墨在打開、攪拌、涂布、晾干、烘干時不小心被曝光;油墨放置時間過長;烘干時間是否符合要求,過長容易引起顯影不凈;顯影時的溫度低、藥水的濃度低、過板的速度過快等都會造成顯影不凈。
不良影響:導致線路連在一起,形成短路,無法使用。還有導致線路開路,無法使用,若無法返工,將會延長交貨周期。
規避措施:確保線路油墨的存放環境不被外面的光照射;顯影的強風按照SOP規定值;根據SOP的參數調整溫度,藥水濃度以及過板速度。
5.內層偏移:內層對位對準度不夠,合內層圖形向一方偏移。
不良原因:在對位中上下夾在一起的時候,沒對準導致偏移;內層有漲縮。
不良影響:造成后期開短路都有可能,交期也會跟著受影響
規避措施:對位的時候,兩面菲林要對準蝴蝶pad;二次元然后根據系數做漲縮。
6.內層蝕板不凈
不良原因:氯離子濃度太高了;PH值太低;蝕刻壓力不夠;蝕刻速率太快。
不良影響:這會產生短路,過AOI時也可以發現,然后進行修補,
規避措施:降低氯離子濃度;提高PH值;根據SOP調整蝕刻壓力和蝕刻速度。
7.短路:兩條原本不相連通的線路相連了。不良原因:基材不穩定,其熱膨脹系數與銅箔的差異較大;內層蝕刻過程產生末蝕刻掉的殘銅點;各工序定位不準,內層孔位偏移等。不良影響:短路無法使用,需要用刀片劃開短路區域,或者做返工蝕刻。返工蝕刻會將線路比原來要細一點。規避措施:基材與銅箔的熱膨脹系數基本匹配;內層蝕刻后采用光學測試儀檢測殘銅;采用定位銷、四槽孔定位等方法,提高定位、孔位精度。
8.內層擦花開路
不良原因:在沒蝕刻前,把表層的藥水在轉板的時候擦掉了,導致沒抗蝕性,直接開路報廢處理。
不良影響:直接開路了,而且不能修補,需重新補料生產,交期會延后。
規避措施:在轉工序的時候,和加工操作的時候,需要避免擦花。
三、壓合不良
9.壓合流膠不良
不良原因:壓合鋼板污染;PP片過期,流動度偏高,導致流膠嚴重;壓合參數設置不正確,溫度過高導致流膠嚴重;壓合參數設置不正確,壓合壓力過大導致流膠嚴重。
不良影響:流膠太多會導致缺膠,爆板分層。如果做成產品會造成傳輸信號不良。
規避措施:壓合鋼板做好清潔;檢查來料是否合格;根據SOP對溫度和壓力做調整。
10.壓合起泡:多層板金屬層與樹脂層之間或各玻纖布間的局部區域發生膨脹有分層。
不良原因:這跟壓合參數和pp片有關系。
不良影響:不可預測的電性不良,電磁干擾控制下降,使用壽命降低。
規避措施:嚴格根據SOP作業指導書合理調整參數和檢查來料情況。
11.壓合凹痕:板面出現一條凹槽,壓合完成品常有些不良出現。若是線路上的凹點需做補線處理。
不良原因:壓合時,材料表面有異物;缺膠;棕化處理不到位。
不良影響:影響美觀,嚴重的會導致不同層之間信號短路,如果凹點在線路上會導致開路。
規避措施:壓合前做好棕化處理;排板時也要注意操作手法,和現場的7S需要做到位。
12.板翹:一般要求PCB翹曲度小于0.75%。
不良原因:pcb單片很長,寬度很小,拼set時鏤空位大,導致沒有支撐位,懸空過大,導致板翹。
不良影響:造成后期貼片不能刷錫膏,和上自動貼片機。
規避措施:出貨前壓板,可以減少板翹;確保表面銅的均勻性,和壓合結構設計對稱;調整SET拼板,增加支撐面積,減少板翹;能改板厚最好。
13.靶孔偏移:偏移不超過0.05mm。
不良原因:在打靶的時候,沒抓準靶心,導致打偏。
不良影響:后期做內層無法對位,需采用備用靶標,做二次打靶。
規避措施:在做激光打靶的時候,需要對準靶心精準打靶。
14.內層擦花
不良原因:棕化中沒有交叉放板導致擦花;壓合排板過程中擦花。
不良影響:影響外觀,嚴重的可能會將線路擦斷,造成開路。
規避措施:檢查棕化后水洗段及烘干段之滾輪是否太臟,有異物卡在上面或者滾輪跳動。
15.沖床壓傷
不良原因:模具成型時彈出碎屑,將線路壓傷。
不良影響:造成線路露銅、氧化。
規避措施:在模沖之前,需要保持表面清潔、沒有雜物,再進行模沖。
16.異物入板內
不良原因:6S環境造成有異物進入板內。
不良影響:影響外觀。
規避措施:生產前做好6S環境處理。
四、鉆孔不良
17.鉆孔偏孔
不良原因:疊板太厚;板件雜物;蓋板不好;下鉆速度過快;主軸的搖擺度。
不良影響:鉆偏鉆孔與導線連接點會變少,層與層直接的連接信號不穩定。
不良措施:做好首件外觀檢查,檢測設備是否異常。
18.鉆孔不透
不良原因:鉆孔時斷刀后,沒繼續再鉆此孔,導致沒鉆穿的現象;鉆孔的疊板張數過多,導致沒鉆穿。
不良影響:導致后期開路,層與層之間無法導通。
規避措施:鉆孔中發生異常,需要核對是否漏鉆或者多鉆。
19.漏鉆孔
不良原因:鉆咀斷刀后,沒找到從哪里開始斷刀,直接換鉆咀重新鉆了。導致多個孔漏鉆。
不良影響:漏鉆導致層壓層之間無法連接,也是致命的。且需要補料重新生產。
規避措施:在鉆孔中發現有設備異常或者斷刀停電等,加工中的所有板需拿首件核對,避免多鉆漏鉆。
20.多鉆孔
不良原因:CAM工程師在處理資料時,將孔加到線路上了且沒做開短路分析;優化鉆孔資料排版時造成。
不良影響:導致開路,或者將其他焊盤會鉆掉,需重新補料生產。
規避措施:CAM工程是制作過程中需按作業指導書制作,制作完成時需跑網絡分析或者核對原搞有IPC網絡的需核對IPC網絡;若是生產中優化鉆孔資料誤將鉆孔復制到其他單元了,優化完后需核對單元總孔數是否和實際資料相符,并做首件檢查。
21.爆孔
不良原因:材料原因;模具沖孔沒加引導孔,導致爆孔。
不良影響:嚴重的會導致分層,一旦分層影響到線路就會造成信號不良。
22.孔損
不良原因:鉆咀偏位導致孔損,導致后期裝配卡槽不穩;疊板張數過多導致;因為槽孔孔密,轉速快了后就會鉆到一半斷刀,造成孔損。
不良影響:造成后期裝配卡槽裝不進去(槽長變短)。
規避措施:減少鉆板的張數;調整轉速,不要過快。
23.定位孔損
不良原因:成型鑼板時用此孔做了定位,造成孔拉傷。
不良影響:影響外觀,表面露銅氧化。
規避措施:做定位時優先選擇無銅孔,且是基材上的獨立孔最佳。做定位時要采用正確操作手法。
24.暈圈
不良原因:因機械加工外力的影響造成基材表面上或內層樹脂的破碎,或微小分層裂開,但多數會出現在孔邊緣,或是受到機械加工的位置。
不良影響:孔徑已經發生改變,影響裝配。
規避措施:采用新鉆咀生產,降低鉆孔的給速,在一鉆工序完成。
五、線路不良
25.線細
不良原因:曝光不當造成影像轉移不良;蝕刻過度都會產生線幼。
不良影響:可能導致斷線,造成信號傳輸不穩定或者中斷。
規避措施:根據SOP對應的底銅厚度,合理調整曝光、蝕刻參數等。
26.線路鋸齒
不良原因:圖形轉移時干膜貼的不實造成在電鍍過程中滲鍍或蝕刻過程滲漏造成。
不良影響:造成線路,線寬不等寬,局部還會發生線幼。
規避措施:干膜滾輪的壓力是否合格,根據板厚做調整,做首件檢查。避免批量性問題產生。
27.撕膜不凈引開路
不良原因:顯影前,干膜上的離心膜沒撕徹底,造成圖形被蓋住,顯影不完整。
不良影響:導致開路無法使用。
規避措施:在放進顯影傳送帶時,需要兩面看清楚是否完全撕掉,確保離心膜撕干凈。
28.撕膜不良易滲銅
不良原因:在線路前處理階段,未能將銅箔的氧化層處理干凈,壓膜后導致結合不佳,或者,在線路轉電鍍過程時間太長,導致干膜內銅箔氧化,一般不允許超過24H!
不良影響:造成短路,修板厚補線會影響外觀。
規避措施:根據實際產生的原因來做規避,如果是磨板造成的,需要調整參數,以及壓干膜的操作手法,還有滾輪的松緊度。
29.曝光垃圾引短路
不良原因:機臺上清潔不到位,短路不能使用。
不良影響:短路了就不能繼續往下做了,需要做返工菲林去蝕刻。
規避措施:需要做好曝光臺的清潔工作。
30.曝光露銅上錫
不良原因:菲林上有垃圾或菲林使用壽命無管控。
不良影響:導致曝光顯影后露銅,電鍍鍍上銅和錫,造成殘銅。
規避措施:檢查菲林,如砂眼;還有就是是否變形。
31.補線不良
不良原因:斷線后,補線不到位造成的。
不良影響:可能造成線路脫落,后期開路。
規避措施:要從源頭控制,盡量做到不補線,保證良率。
六、電鍍、刻蝕不良
32.電鍍夾膜
不良原因:電鍍夾饃是因為電鍍時間太長或者電流強度太大造成鍍銅太厚,包裹了旁邊的感光膜造成的。
不良影響:造成了短路了,后期無法使用
規避措施:根據銅厚打電流,合理優化線路寬度,保證間距。
33.電鍍甩層
不良原因:
- 銅箔微蝕過度或不足;
- PCB流程中局部發生碰撞,銅線受外機械力而與基材脫離;
- 板面清潔度不足;
- 活化不夠或加速過量;
- 沉銅藥水含量比例失調;
- 一次鍍銅前停放時間過長,板面過度氧化,除油酸洗未達到效果;
獨立線沒多補償,也會造成這種情況。
不良影響:可能會導致短路。
規避措施:獨立線多補償,客戶允許的情況下,在旁邊鋪方形銅塊,然后做接地。
34.焊盤殘缺
不良原因:阻焊開窗設計問題;菲林有問題;曝光不良。
不良影響:導致后期貼片不良,焊不到錫。
規避措施:優化好阻焊開窗,檢查好菲林。
35.銅面粗糙
不良原因:鍍銅槽本身的問題,如陽極問題、光澤劑問題、槽液成分失調或雜質污染等;PTH制程帶入其他雜質,如活化成分失調鈀濃度太高或者預浸鹽殘留板面、化學銅失調板面沉銅不均等。
不良影響:后面做表面工藝也會粗糙,不平整,貼片焊錫會不良。
規避措施:根據SOP規范操作,生產板子前對設備進行點檢,避免雜質污染。
36.滲鍍
不良原因:干膜和銅箔結合度不佳導致滲鍍;銅箔的氧化層處理不干凈;線路轉電鍍過程時間太長,導致干膜內銅箔氧化;電鍍銅缸水失調,水攻擊干膜導致滲鍍;電鍍處理時大氣壓力太大或震動馬達振幅太大。
不良影響:會導致短路,斷路,屬于致命問題。
規避措施:選擇好的酸性除油劑;鍍錫槽確保陽極面積足夠;控制鍍液錫光劑的量,避免過量;濕膜鍍純錫板要存放在環境相對較好的車間,存放時間不能超過72小時等。
37.蝕板過度
不良原因:浸泡和鼓泡式蝕刻會造成較大的側蝕;蝕刻速率過慢會造成嚴重側蝕;堿性蝕刻液的PH值較高時側蝕增大;堿性蝕刻液的密度太低會加重側蝕;銅箔越厚在蝕刻液中的時間越長,側蝕量就越大。
不良影響:導致線寬變細工寬度不均勻,影響信號傳輸,容易引起地彈、反射等現象,如果發生在電源走線上,會導致過電流能力下降。
規避措施:根據對應的問題做改善,前提是找到真正的原因,如銅箔厚度,根據底銅厚度,做相應的補償。
38.孔內銅渣
不良原因:鉆孔后孔內有粉塵、底板的碎屑,化學銅加工時這些粉塵上會沉積化學銅形成銅渣。
不良影響:影響塞孔和孔銅厚度。
規避措施:改善鉆孔制程和高壓水洗清潔能力。
39.光學點脫落
不良原因:光學點太小(如0.4mm、0.5mm),沒加保護環;銅箔剝離強度偏低等。
不良影響:影響SMT定位。
規避措施:加保護環;同時對大光學點做銅厚補償,2oz的需要加到大1.3mm左右。
40.金面氧化
不良原因:若是還沒有鍍金時的鎳面氧化,出現這種情況基本上是沒有辦法處理;若是鍍金后的氧化,造成氧化的原因是金缸內鎳、銅離子超標,或者鍍金時間只有3~5秒的情況下,金層沒有把鎳面蓋住,引起底層鎳氧化。
不良影響:氧化后導致無法焊接。
規避措施:每個班次在生產前需要檢驗藥水,合格后才能進行生產,同時要確保鍍金時間充足。
41.錫面粗糙
不良原因:銅面粗糙;噴錫的時候錫爐內雜質多;噴錫后未及時過風床而致使板直接和其它地方接觸造成有粗糙現象!
不良影響:導致后期出現假焊,虛焊!
規避措施:在噴錫前檢查是否有銅面粗糙。
七、檢測、成型不良
42.V-CUT上下刀錯位
不良原因:V-cut刀具調整不到位,導致漏銅甚至開路風險。
不良影響:露銅需要做補油處理,嚴重的會做報廢處理。
規避措施:在V割前需要做首件確認,保持上下刀具在一條水平線上,不能錯開。
43.V槽漏割
不良原因:生產文件轉化異常;生產程序遺漏。
不良影響:會導致后期無法分板,如果貼片后就很難去V,損失很大。
規避措施:做首件確認,確保每個V-cut處都被V割了,且深度要根據板厚做調整。
44.V偏傷銅
不良原因:放板的時候沒放好,導致偏位,造成線路V斷或漏銅。
不良影響:傷銅厚線路會漏銅氧化,還會把線V斷,需要重新補料。
規避措施:V割時需要注意操作手法。注意軌道是否有異物,需要放平。另外要保證板子邊緣是平行的。
45.V深不良
不良原因:V割刀上下太緊,導致V的太深,容易斷板。
不良影響:會很容易斷板,造成后面SMT貼片困難,也會影響效率。
規避措施:做首件確認,根據板厚調整V割的深度。首件確認好之后再進行V割。
46.斷板
不良原因:連接位太小,油票孔間距需要大于0.25mm以上,否則太近容易斷,尤其是薄板。
不良影響:導致SMT無法按照整片拼板生產。
規避措施:調整郵票孔間距,常規是0.3mm間距左右。
47.斷工作邊
不良原因:V割太深,導致一碰就斷;另外可能剛好撞到了。
不良影響:沒有工藝邊過不了軌道,會卡住。斷了就只能手工去焊接,會很麻煩。
規避措施:控制好V割深度,手工嘗試去掰,前提是做首件確認,OK后再繼續往下生產;后工序也需要輕拿輕放。
48.鑼壞
不良原因:銷釘的問題;工程師畫鑼帶的時候畫偏;沒按半孔處理。
不良影響:會有殘銅卷入孔內,造成裝配,影響焊接。
規避措施:做半孔工藝,改起刀點。
49.OSP板污
不良原因:OSP前焊盤擦花有異物、焊盤有擦花、OSP后有錫進入到板內。
不良影響:貼片無法上錫,導致后期焊錫不良,影響外觀。
規避措施:OSP后不要有異物接觸到板內,包括手指印。
八、阻焊不良
50.阻焊上PAD
不良原因:對位偏位或開窗過小,導致后期無法焊接。
不良影響:影響上錫性,導致報廢,或對后續SMT生產造成困擾。
規避措施:生產前檢查設計資料,批量前做首件檢驗。
51.露銅問題
不良原因:不當操作導致擦花露銅。
不良影響:導致產品報廢,或降低終端產品的壽命。
規避措施:對生產中的操作進行預先梳理優化,針對性輸出防范措施。
52.阻焊顯影不凈
不良原因:預烤相關:預考時間過長、溫度過低或過高;顯影相關:顯影速度過快、噴壓過低,顯影液濃度過低、后段水洗不足。
不良影響:影響上錫性,導致產品報廢。
規避措施:嚴格把控預烤和顯影工序,規范操作。
53.掉綠油橋
不良原因:油墨問題、曝光不良或者顯影時被沖掉了、IC橋超出工藝制成能力,導致后期焊接連錫。
不良影響:增加SMT時的連錫短路風險。
規避措施:設計時專門點檢,生產時先做首件。
54.綠油擦花
不良原因:表面擦花,導致線路上金。
不良影響:造成SMT時連錫短路風險。
規避措施:對生產中的操作進行預先梳理優化,針對性輸出防范措施。
55.綠油拍反
不良原因:對位的時候,和線路對反,不能使用,報廢處理。
不良影響:產品報廢。
規避措施:生產前做首件檢驗,生產時做好自檢。
56.綠油起泡
不良原因:印油后未充分靜置就拿去預烘了,里面有空氣沒有溢出,受熱時內部空氣膨脹成氣泡。
不良影響:導致產品報廢。
避免措施:印油后,油墨需要靜放20~30分鐘,使內部空氣溢出,避免受熱產生氣泡。
57.綠油入孔
不良原因:顯影速度問題,或者孔太小導致油墨沖不掉。如果是插件孔后期無法插件。
不良影響:導致報廢,或影響后續DIP時正常使用。
避免措施:設計點檢規避,生產首件確認。
58.綠油脫落
不良原因:油墨問題,導致露銅氧化。
不良影響:導致產品報廢,或在使用后,影響成品使用壽命。
避免措施:阻焊烘烤后,做附著力測試。
九、文字不良
59.文字不全
不良原因:網版不下油,或者操作員手法問題,造成文字不全。
不良影響:不夠美觀,無法看全絲印,漏掉電路信息。
規避措施:嚴控網版下油流程;進行員工培訓,務必做到合格操作。
60.文字模糊
不良原因:文字沒有放大和優化間距;絲印網太稀,下油過多;網版不干凈、滲油、油刮力度不足、掉油;還有后工序烘烤溫度、油墨問題等,都可能造成文字模糊不清。
不良影響:判斷不清影響后期加工,如插件錯誤、加工效率低等;絲印無法分辨還會影響日后電路板調試問題;不夠美觀。
規避措施:生產前優化設計圖的絲印大小與位置;檢查好網版;采用優質油墨等。
61.文字印反
不良原因:絲印資料用錯,造成文字印反。
不良影響:不美觀。
規避措施:生產前檢查好絲印資料。
62.文字印偏
不良原因:
- 印板時沒掛上防呆孔,造成文字印偏;
- 所鉆的或沖的工具孔準確性不好;
- 板彎板翹導致印刷偏離;
- 調整各有關環境間的差異;
- 絲網的離板距離不當;
- 刮刀壓力不理想;
使用的是非固定框,也容易產生印字偏移。
不良影響:貼片、人工插件、板子測試時判斷不清,可能會導致插件錯誤以及影響效率。
規避措施:掛防呆孔;采用準確性好的工具孔;使用固定框;調整絲網的離板距離等。
看到這里應該是“真愛”了
記得收藏點贊哦~
華秋電路提供1~20層PCB制造服務,高可靠、短交期!
四層板板材費僅需499元/㎡
HDI特價體驗500元/款
如果您有 PCB 板的生產需求,歡迎來華秋電路打樣體驗,相信不會讓您失望!?點擊免費打樣
-
pcb
+關注
關注
4326文章
23160瀏覽量
399942
發布評論請先 登錄
相關推薦
PCB及PCBA失效分析的流程與方法
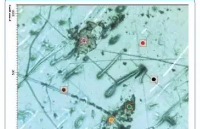
評論