根據車間模型生成排產計劃的一般程序可簡單地描述為下面6個步驟。
1. 建模
車間模型必須詳細地捕捉生產流程的特征和相應的物流,以便以最小的成本生成可行的計劃。由于一個系統的產出率只受潛在瓶頸資源的限制,因此,我們只需對車間現有全部資源的一部分,即那些可能成為瓶頸的資源,建立一個清晰的模型。關于建模方法的細節我們將在后面進一步闡述。
2. 提取所需數據
生產計劃排程使用的數據來自ERP系統、主生產計劃和需求計劃。生產計劃排程僅利用這些模塊中可用數據的一個子集,因此,在建立一個給定生產單元的模型時,必須指明它實際需要哪些數據。
3. 生成一組假定(生產狀況)
除了從ERP系統、主生產計劃和需求計劃這些數據源中接收的數據之外,車間或生產單位的決策者或許對車間當前或未來的狀況會有更進一步的知識或期望,這些信息在其它地方(如軟件模塊中)是不能得到的。再者,對車間的可用能力或許也可以有多種選擇(如柔性的倒班安排等)。因此,決策人員必須有能力修改數據和建立某種生產狀況。
4. 生成一個(初始)排產計劃
在有了模型和數據之后,就可以針對給定的生產狀況,利用線性規劃、啟發式算法和基因算法等各種復雜的優化方法來生成排產計劃。這項工作可以一步完成,也可以通過兩級計劃層次(先綜合的生產計劃,后詳細的排產計劃)完成。
5. 排產計劃分析和交互修改
如果通過兩級計劃層次完成,也即先生成綜合資源的上層生產計劃。那么,在生成一個詳細的排產計劃之前,人們或許首先要對這個生產計劃進行分析。特別地,如果生產計劃不可行,決策人員可以交互地指定一些計劃途徑來平衡生產能力(如增加班時或指定不同的加工路徑)。這或許要比修改在單個資源上的加工工序(下層排產計劃)更加容易。APS采用了例外管理(management-by-exception)的技術,如果出現問題和不可行性(如超過定單交貨期或資源過載),APS就會發出警告(alerts)。這些警告首先被“過濾”,然后,正確的警告被傳遞到供應鏈中正確的組織單位。此外,針對一種生產狀況產生的排產方案還可以通過結合決策者的經驗和知識交互地改進。當然,為了提供真正的決策支持,必要的修改次數應當受到限制。
6. 生產狀況核準
當決策人員確定已經評估了所有可選方案時,他/她將選擇那個體現最佳生產狀況的排產計劃去執行。
7. 執行和更新排產計劃
決策人員選定的排產計劃將被傳遞給:MRP模塊(分解計劃)、ERP系統(執行計劃)和運輸計劃模塊(在顧客定單完成時安排裝運車輛)。MRP模塊把在瓶頸資源上計劃的所有活動分解成在非瓶頸資源上生產的那些物料或由供應商交付的物料;此外,對某些加工定單所必需的物料也將被預定。排產計劃將持續執行到某個事件信號發生時才進行更新,也即直到修改一個排產計劃看來是可取的時候。這個事件可以是一個新定單的到來、機器故障或凍結的計劃部分已執行完畢(后面我們還將對排產計劃的更新作詳細討論)。改變車間生產模型的情況不太經常。如果結構保持不變和只是數量上受到影響(例如一個機床組中的機床數或某些已知產品的新變種),那么,通過下載ERP系統中的數據,APS能自動更新模型。但當變化很大時(例如具有某些新特征的新生產階段的引入),那么,由專家對模型進行手動調整則是可取的。
審核編輯 黃宇
-
ERP
+關注
關注
0文章
510瀏覽量
34477 -
APS
+關注
關注
0文章
337瀏覽量
17576 -
MRP
+關注
關注
0文章
13瀏覽量
6060
發布評論請先 登錄
相關推薦
安達發|APS高級排程高級物料需求計劃
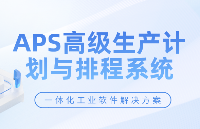
燈具照明行業APS智能計劃排產系統解決方案
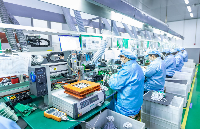
APS生產排產在電子煙行業的運用分析
安達發|APS生產排程軟件6大核心技術
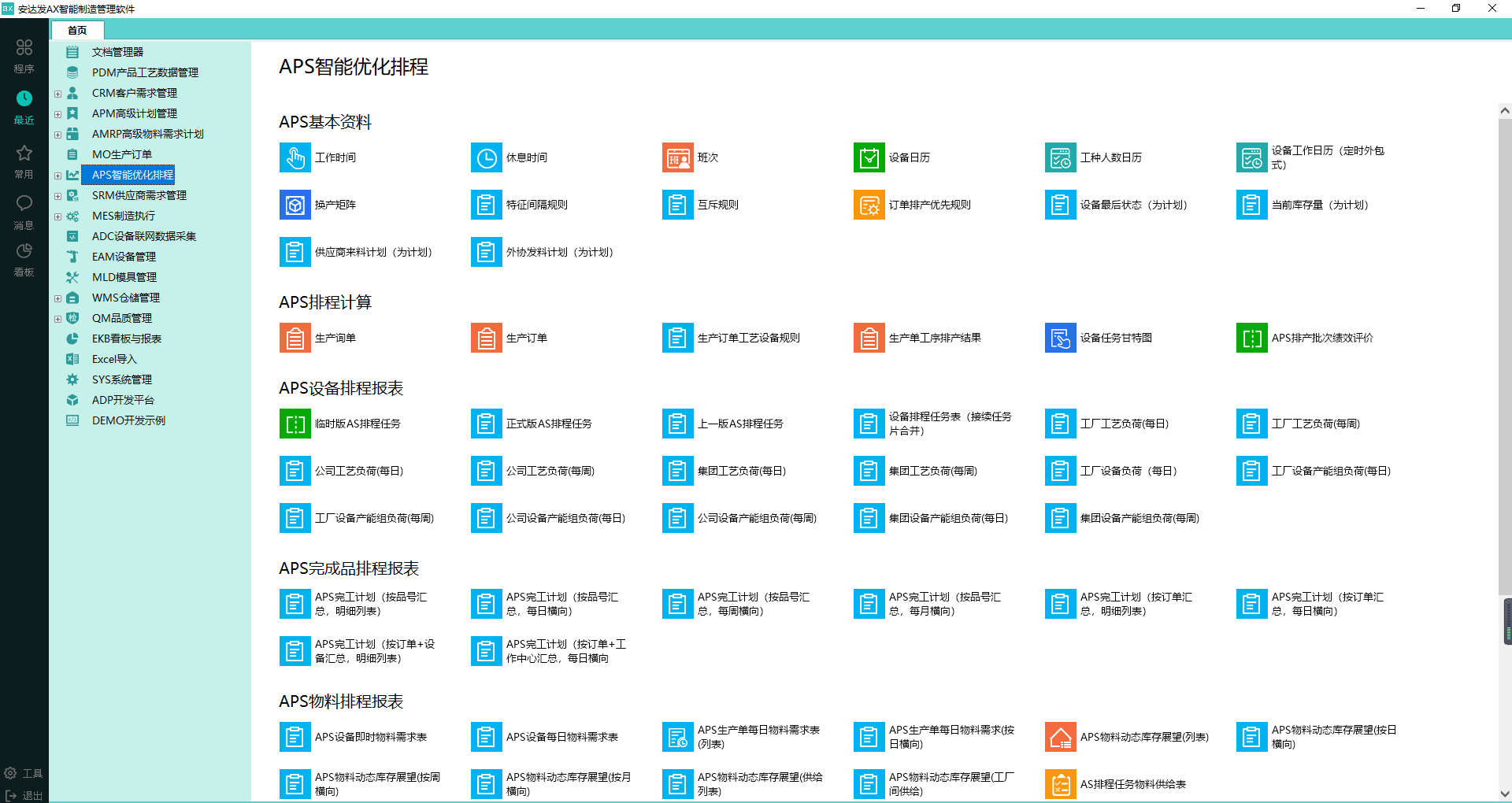
評論