摘要
全固態電池的研發是為了“防止被顛覆”,其產業化需以市占率突破1%為標志。
自推進以來,全固態電池的必要性和產業化始終是備受爭議的存在。
全固態電池的研發是為了“防止被顛覆”,其產業化需以市占率突破1%為標志。在近期舉辦的全固態電池創新發展高峰論壇上,中國科學院院士、清華大學教授歐陽明高發表了上述觀點。
論壇上主流觀點認為,全固態電池產業化較可能在2030年取得突破。由于固態電池可同時滿足高安全性、高能量密度、高功率、高溫度適應性等,且材料選擇的范圍更高,具備“顛覆”液態電池的潛力。
不過,目前國內發展全固態電池產業面臨的挑戰是巨大的,具有跨學科的特性、技術門檻極高,包括材料界面、工藝、產業鏈、設備等,需要業界進行協同創新。
為什么需要全固態電池及產業化?
中國科學院院士、清華大學教授歐陽明高指出,固態電池相對于液態電池是顛覆性技術,行業應提高重視程度、積極研發,以防范風險。
首先,動力電池行業雖然已進入產能過剩的階段, 電池成本不斷下降,但并沒有完全滿足終端電動汽車客戶的需求,如怎么在全壽命周期內不析鋰、不影響壽命、不發生安全事故,低溫續航,如何解決硅負極膨脹率高的問題、以提高負極中硅的含量、最終提高體積能量密度(磷酸鐵鋰電池)等。
其次,在新一輪技術創新周期中,行業已卷向“提質降本增效”,需要通過材料換代來實現。例如,行業內對于比能量的追求,并不單純是提升比能量,而是在期待“比能量提升的同時,成本不需要提升太多”的顛覆。因此,行業需要居安思危,電池需要平衡的性能體系,全固態電池具備技術“顛覆”的潛力。
東風汽車集團有限公司研發總院副院長史建鵬同樣認為,包括安全性、里程焦慮、能量密度在內的液態鋰電池三大痛點,受到現有材料體系已接近能量密度上限因素的限制,本質上沒有得到解決。
此背景下,產業希望構建新一代動力電池。其中,由于采用了固態電解質(不易燃、耐高溫、化學活性低),固態電池能大幅提升電池安全性;又因為固態電池可兼容高比能正負極,將打開能量密度天花板,故有望成為動力電池下一輪技術競賽的關鍵。
南方科技大學教授許曉雄認為,高安全、高性能、低成本是鋰二次電池產業發展的必然趨勢,高性能要求則囊括了高能量密度、高功率(可快充)、長壽命等,全固態電池有望實現以上高性能要求。
弗迪電池首席技術官孫華軍則提出,全固態電池產業化能帶來哪些價值,需要對標2030年液態電池會是什么狀態來思考,液態電池也在持續改進;而且要從系統層級來思考,囊括如重量能量密度、體積能量密度、成本維度等。
2. 全固態電池的量產標志是什么?
從全球全固態電池產業化路線圖來看,產業化時間聚焦在2027-2030年。
歐陽明高進一步指出,較為合適的產業化定義是全固態電池市占率達到1%。參照2023年2000萬左右的電動汽車銷量預期來看,即全固態電池裝車量超過20萬輛。
而一汽研究院院長王德平認為,全固態電池在2027或2030年的產業化,可能只是達到一定程度的小規模、小批量的示范性裝車。對固態電解質等關鍵問題的突破,有望加速產業化的進程。
孫華軍認同上述觀點并表示,新電池技術的應用遵循一定規律,如鋰電池先應用在電子消費產品上,經過長時間積累后才過渡到動力電池產品。按此推算,固態電池也應該先在其他領域應用,再逐漸擴展至電動汽車。
另據孫華軍披露,比亞迪10年來持續進行著固態電池的研發,主要走硫化物路線,目前已可實現保留10%電解質的相關產品。
3. 全球固態電池產業布局呈現出何種差異性?
歐陽明高總結,從全球固態電池產業布局來看,中國企業最多,然后是日本、韓國,實力強勁。美國主要是一些創業企業,與歐洲合作廣泛。
日本在電池與整車性能匹配結合方面較有優勢,已經搭建起官-產-學聯盟。如豐田、本田、日產,同時進行全固態電池研發和整車生產,其中豐田的研發進度最為深入。
韓國三大電池廠在全固態電池方面已取得實質性進展,尤其是三星,國內部分團隊的任務之一,便是復現三星的全固態電池。
美國以創業企業為主導,缺少車企、電池廠的力量,一方面靠資本市場支撐,一方面則靠歐洲車廠的合作,如Solid Power和寶馬合作等。
中國的固態電池技術路線相對多元化,以固液混合為主,以氧化物路線為主導。目前,國內半固態電池池正在試裝車,但是良品率、電池成本、充電倍率、循環壽命這些問題還需要解決。
全固態電池技術方面,國內外專利布局存在較大差距。豐田有超過1300項相關專利,截至2023年10月,國內公司有關全固態電池的專利未超過100項。
4. 固態電池整體上面臨什么挑戰?
據史建鵬總結,目前固態電池存在四大挑戰。
首先,固態電池所需,不只是在現有三元正極材料體系上去做增量或補充,而是更為復雜的高性能正極材料。短期內,正極材料沿用高鎳三元體系,安全性差且易發生熱失控,長期應向超高鎳、富鋰錳基、高壓尖晶石等材料迭代。關于高電壓下三元正極易產氣導致電池鼓包的問題,解決策略是通過單晶化、氧化物包覆、金屬摻雜等手段進一步提升電壓。
第二,固-固接觸的問題,既導致鋰離子傳輸電導率低,也影響電池能量密度,可通過引入電解質膜改性等策略來解決。而現有設備難以支撐制備20μm以下電解質膜,疊加上材料復雜,成本高居不下。 三是相應負極材料的開發。硅負極在充放電過程中體積膨脹大,粉化和分層現象嚴重,有待解決。而在鋰金屬負極的開發過程中,鋰枝晶生長、活性鋰不斷消耗,導致可逆性差;另受到工藝設備的影響,超薄鋰金屬負極的制備還存在困難。
第四,固態電池的制造工藝還需優化,部分生產設備需要定制。其中,正負極和電解質膜的生產設備為主要需要改造或全新研發的設備,尤其是中前段設備。疊片設備也需要做相應升級,與傳統液態電池生產設備的共用率約為70%。總的來看,目前搭建一條1GWh液態電池產線的成本約為1.5億,而固態電池產線搭建成本是其2倍。
具體到硫化物電解質全固態鋰電池上,許曉雄指出,該類電池的優勢是能量密度有望超過350Wh/kg、快充性能優、循環壽命長、工作溫區寬等,但同時也面臨著穩定性低、成本高、制造技術三大方面的挑戰。
其中,當硫化鋰價格低至50萬元/噸時,該類電池成本才有可能與液態相當。制造環節的挑戰則集中在干法制備工藝和裝備的突破上。
審核編輯:劉清
-
電解質
+關注
關注
6文章
820瀏覽量
20158 -
全固態電池
+關注
關注
0文章
57瀏覽量
4878
原文標題:全固態與量產的距離:市占率破1%
文章出處:【微信號:weixin-gg-lb,微信公眾號:高工鋰電】歡迎添加關注!文章轉載請注明出處。
發布評論請先 登錄
相關推薦
王東海最新Nature Materials:全固態鋰硫電池新突破
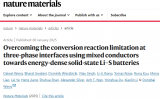
評論